Laser cutting sheet metal has some serious benefits in time savings and accuracy. It can also cause some headaches when cutting holes for direct fastener assembly.
For many years, manufacturers alike have used thread forming screws with standard machine screw threads and case-hardened special points. These screws use pre-made holes, forming their own threads into the mating material. The thickness of the material generally dictates the size of the hole needed to create the lowest driving torque and highest stripping torque which leads to the best joint performance.
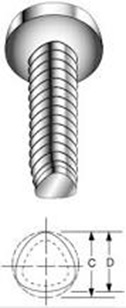
Drilling or punching into mild steel creates holes for these screws. Hole size recommendations exist for each size and thickness of the material. But, when laser cutting holes, we often see the heat affected zone, which makes the surface of the material around the hole somewhat harder. If using standard hole recommendations for drilling or punching, problems can occur during assembly.
Common Assembly Problems:
- Hard start – screws spin
- High drive torque – gun will not seat screws
- Breaking screws before seating
These problems usually show that the hole size is too small. With oversized holes, we often see threads stripping rather than achieving their assembly torque.
While it is difficult to provide recommended hole sizes for each material type, each thickness, and each method of preparation, performing a drive/strip torque test in a controlled environment may be the best way to ensure the best joint performance. Let’s look at an example of a test recently done by a Bossard engineer:
Plate steel provided by the customer with incrementally larger sizes of laser cut holes:
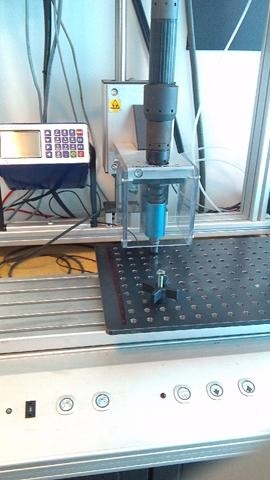
Graph of a typical test:
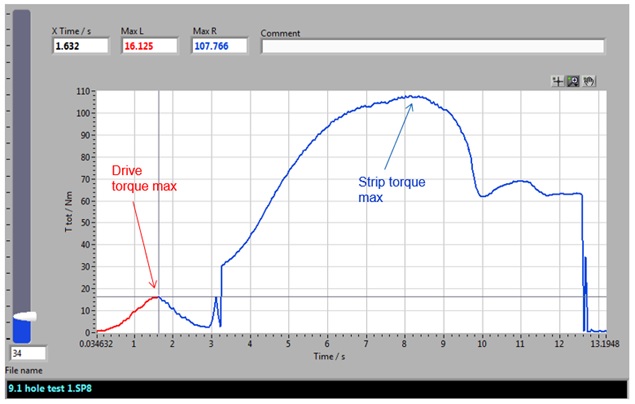
Graph of the average data for many hole sizes:
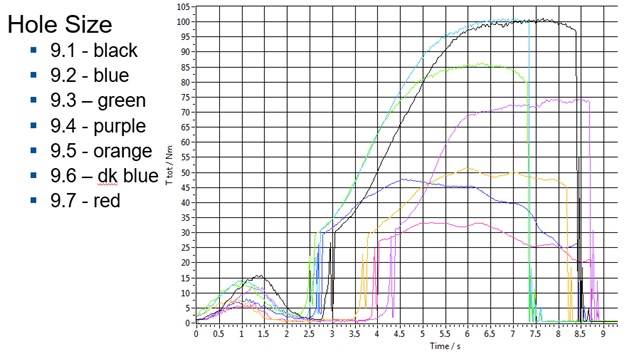
Typical summary data from one hole size:
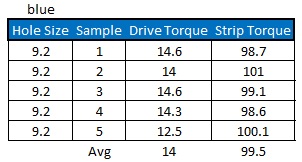
By performing a joint analysis in our laboratory, we can recommend the proper hole size for your design to ensure optimal performance.
If you have interest in any type of joint analysis, check out Bossard’s latest Assembly Technology Expert services, especially the Expert Test Services pillar, or contact us at ProvenProductivity@bossard.com.
Doug Jones
Applications Engineer
djones@bossard.com