There are three basic requirements for fastening technology that apply to just about every industry:
- On the one hand, the fastening and joining function should be guaranteed over the entire service life of the product.
- On the other hand, a simple and safe processing method is essential during production.
- And finally, the solutions should be cost-effective and yet of high quality
With fastening solutions from the field of blind rivet technology, we offer fasteners that meet all three requirements and also offer additional advantages:
- One sided access
- One of the main arguments in favour of blind rivets is that the process only requires one-sided access. Compact tools are available for this purpose. This is a huge benefit because fastening solutions normally are requiring two-sided access, their integration is reduced to work on individual parts or involves considerable set-up costs.
- Different materials can be joined together (mixed materials, plastics, sandwiches etc.)
- Plastic parts
- CRP materials
- Aluminium
- Magnesium
- High density steels
- Sandwich panels
- Prepainted sheets
- Etc.
- Different material thicknesses can be joined with only one rivet
- No special qualifications required
- No thermal load on the workpieces to be joined
- No cooling or curing time required
- No hazardous smoke
The first blind rivet was developed and manufactured in 1934 by “George Tucker Eyelet” in Birmingham, England. What was initially developed as a fastener exclusively for the aerospace industry was soon used in other industries due to its efficient processability and the advantage of one-sided access.
The POP® blind rivet was born.
The KVT-Fastening Group played a major role in the market launch of the POP® blind rivet at the beginning of the 1960s and today has extensive expertise in the field of blind riveting technology. A great deal has happened since then in the development of blind rivets. The latest development in the POP® brand range is the POP® VGrip™. The advantages of this new development are as unique as they are numerous.
- Homogeneous closing head
- An important feature of the VGrip™ blind rivet is the closing head design. During the setting process, the sleeve material is moved radially outwards, resulting in a disc-shaped closing head. In addition, the mandrel head does not dip into the rivet sleeve, which is not the case with conventional multi-range blind rivets.
- This special feature enables the POP® VGrip™ to distribute tensile forces over a considerably larger area on the side of the closing head (see following diagram). As a result, the VGrip™ can absorb higher tensile forces than a conventional multi-grip rivet. In addition, due to the greater load distribution, thinner or fragile sheets can be fastened to the closing head side/blind side without damaging or deforming them.
- An important feature of the VGrip™ blind rivet is the closing head design. During the setting process, the sleeve material is moved radially outwards, resulting in a disc-shaped closing head. In addition, the mandrel head does not dip into the rivet sleeve, which is not the case with conventional multi-range blind rivets.
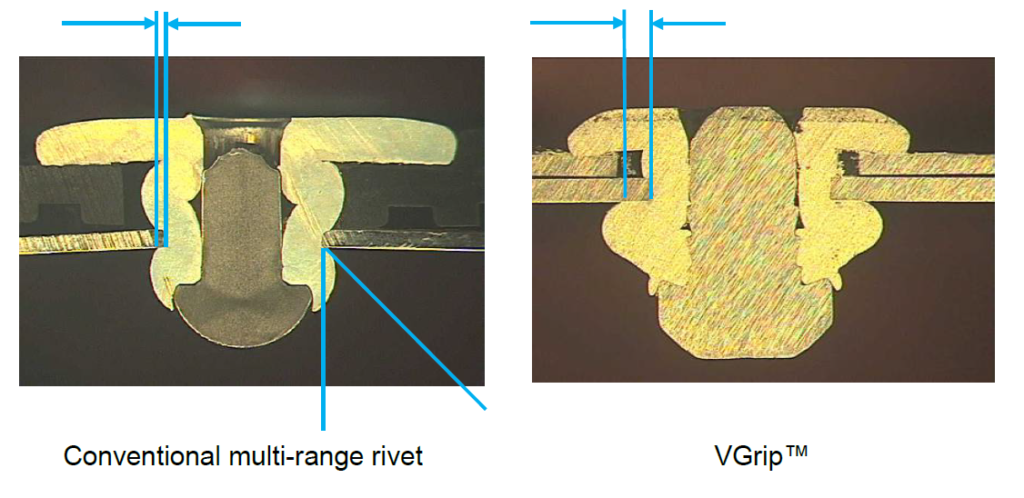
- Increased grip range
- Conventional blind rivets are designed to cover a small specific grip range (application thickness) of components to be joined. For example, four different blind rivets with different grip ranges must be used for different application thicknesses from 1.5 to 6.0 mm. In order to reduce this complexity, the POP® VGrip™ allows a grip range from 1.5 to 6.0 mm to be processed with only one rivet (see diagram below). Thus, four different rivet types are replaced by only one type of rivet.
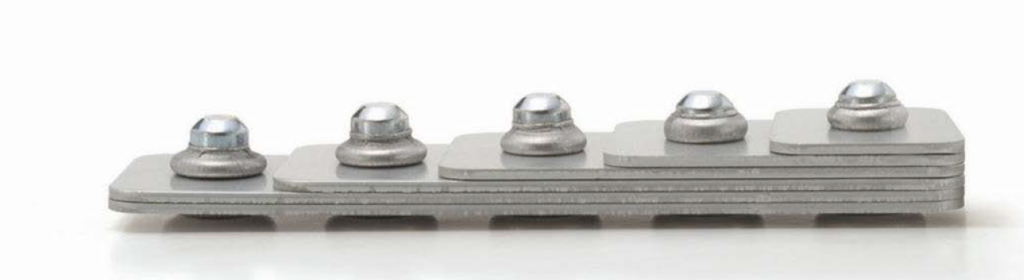
- In general, conventional multi-grip blind rivets work according to the same system and cover the same grip range. However, in comparison to VGrip™ multi-grip rivets within the same grip range do not always form a uniform closing head and can therefore not always absorb the full forces. With certain grip ranges, the closing head cannot form completely, which leads to a slight radial expansion. There is a risk that the connection will be axially loaded (see picture below)
- Controlled bearing stress
- A hole soffit of the rivet sleeve may be desirable, for example, if the bore holes have to be aligned with each other or if it is to be prevented that the components slide sideways towards each other. However, radial expansion is undesirable if it damages the components or if the rivet sleeve material presses between the components to be joined and expands them. (see picture below).
- At VGrip™ in the standard configuration, the rivet sleeve can expand radially to maximize the clamp length range. To limit the radial expansion, the rivet body can be additionally embossed. The workpieces are pulled together securely and the hole soffit force of the components to be joined is reduced.
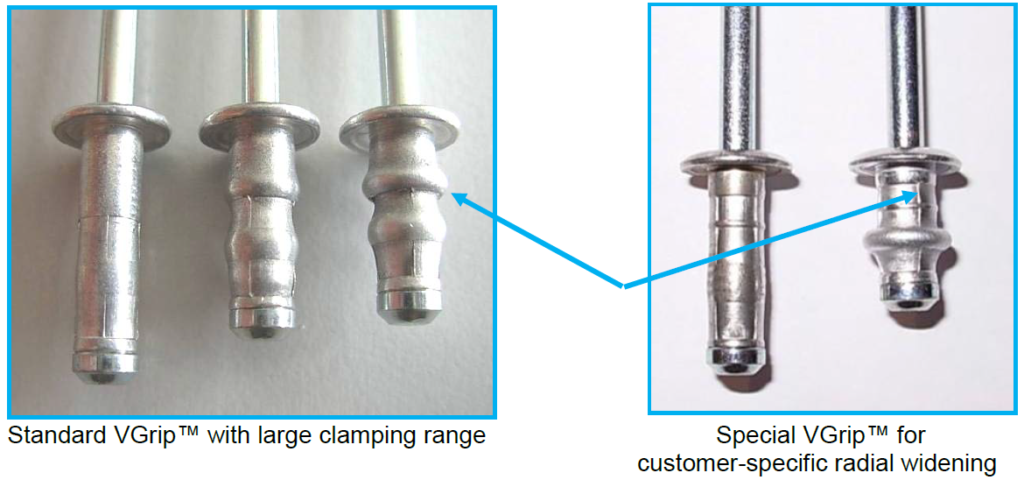
- High clamping force
Based on a modified riveting process, POP® VGrip™ has the ability to close gaps between the joined parts. This simplifies e.g. the work of the workers in production, because they do not necessarily have to close the smaller gaps between two materials to be joined before the riveting process. The VGrip™ with its strong clamping force securely joins the materials and closes the gaps (see graphic below)
- Residual mandrel locking
- Everyone knows it, the clatter of a loose residual mandrel. There are various reasons why the remaining mandrel must not fall out after installation of the blind rivet. On the one hand it reduces the value of a product if something rattles inside, on the other hand it can be relevant to safety, for example in electrical engineering applications, that it must not fall into the interior of the application in order to avoid causing a short circuit.
- With conventional blind rivets, the remaining mandrel is held in the rivet solely by the bead on the rivet head and the deformation on the rivet head. However, the remaining mandrel is not securely locked, e.g. if there are higher tolerances at the mandrel head and at the rivet sleeve, the remaining mandrel can fall out unhindered under vibration or impact effects.
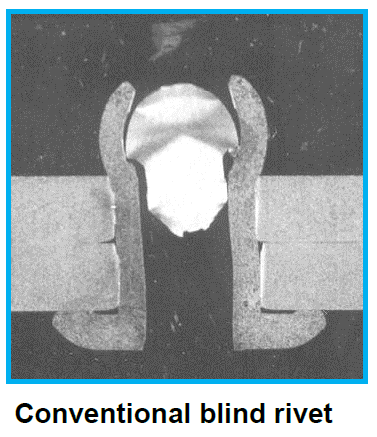
- Due to its design/special mandrel geometry, the POP® VGrip™ features a mandrel locking system which secures the remaining mandrel even in highly vibrating applications and thus prevents it from falling out (see below picture)
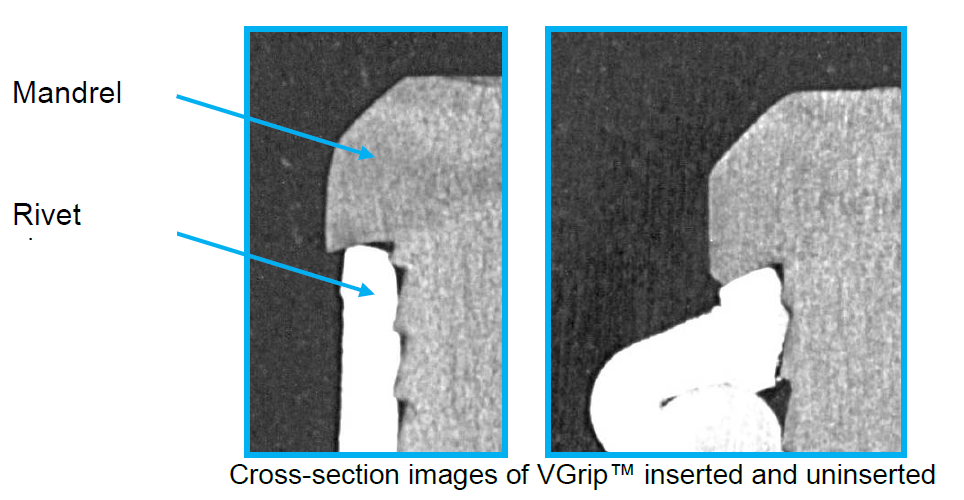
- Rolled mandrel
- To increase the service life of the jaws of the riveting tool, the mandrel is rolled in the tension area.
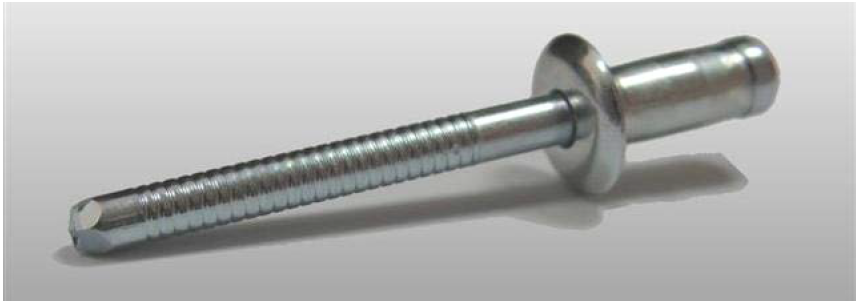
- Special introduction phase
- A bevel at the mandrel head facilitates the insertion of the rivet into the rivet hole and thus shortens the processing time.
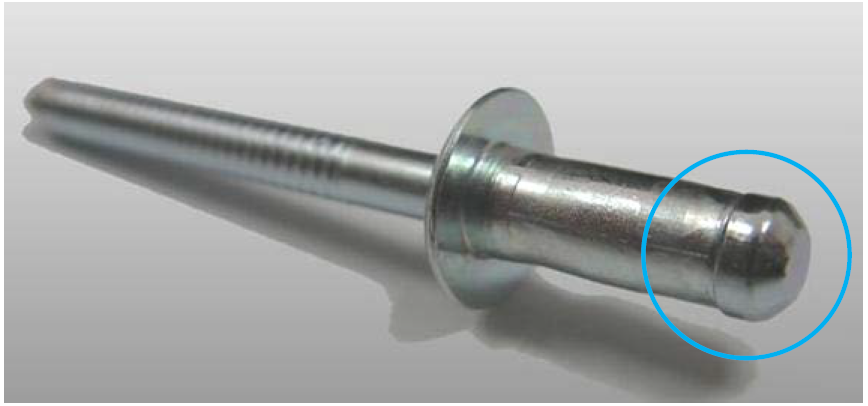
Interested?
Under the following link you can take a look at our current POP® blind rivet assortment and learn more about the POP® brand.
Or watch a video about the advantages of the VGrip™ system on Youtube under the following link.
Do you still have open questions about our POP® brand products or about other products in the riveting technology sector? Then write to us: ProvenProductivity@bossard.com
POP® VGrip™ by Bossard